Commercial Refrigeration Parts & HVAC
Roll forming plays a major role in keeping things cool, from HVAC systems for commercial buildings to frozen foods at the grocery store.
Commercial Refrigeration Parts
The commercial refrigeration market is a growing global market, fueled largely by a demand for ready-to-eat foods. It is expected to grow from nearly $50 billion in 2021 to around $68 billion in 2028.
Roll forming is used extensively to build commercial refrigeration parts. All those refrigerators and freezers you see at the grocery store? They’re built with roll formed components, including:
Textured refrigerator paneling for decorative purposes
Kick plates by the floor that keep dust at bay
Stainless steel handrails
Protective sills
Insulated shelving structures that hold food and beverage
HVAC Systems
The HVAC industry in the U.S. is also growing fast, with forecasts showing a jump from $25.6 billion in 2019 to $35.8 billion in 2030. Demand for more energy-efficient systems and increased construction are fueling this growth.
Several interior and exterior structural parts of HVAC systems are also roll formed. Even the tubing that is part of the refrigerant exchanger in an HVAC system is made of roll formed copper. Roll forming is used to produce:
- Ducts
- Cooling tower louvers
- Dampers
- Filter frame units
- Air conditioner cases
- Electric heater housings
- And more
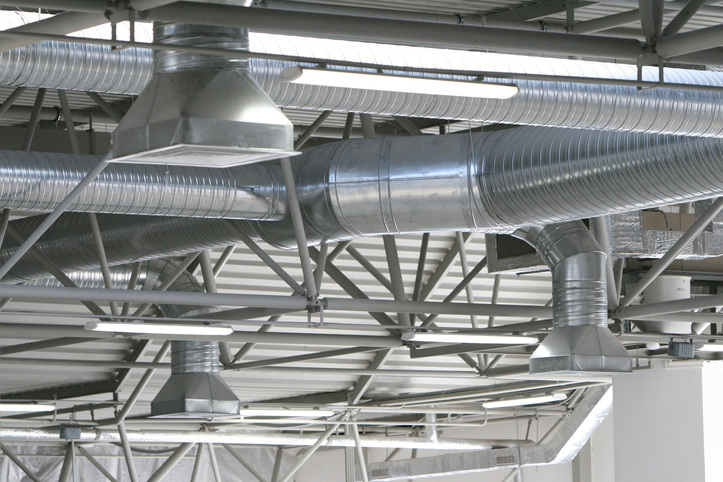
Roll Forming Advantages
Both the commercial refrigeration and HVAC industries need a high volume of long, slender parts – roll forming’s specialty. Roll forming is a highly repeatable process. Once the tooling is in place, roll forming produces components more consistently than other metal shaping processes, even over long runs.
Whether the parts you need are decorative or structural, HVAC and commercial refrigeration parts are perfect for roll forming.
Roll forming allows engineers and designers to create customized components. Whether you’re using stainless steel parts for framing or pre-painted aluminum sheets for decoration, roll forming produces a clean and attractive finish.
Have a complex design? Roll forming can fabricate parts with:
- Complex profiles
- Inline punching for accepting mating parts
- Tricky hole patterns
- Tight tolerances
- Pristine finishes
Hole punching, bending, and cutting to length can easily fit into one continuous process rather than separate steps. Roll forming is a more cost-effective and productive method in all these cases.
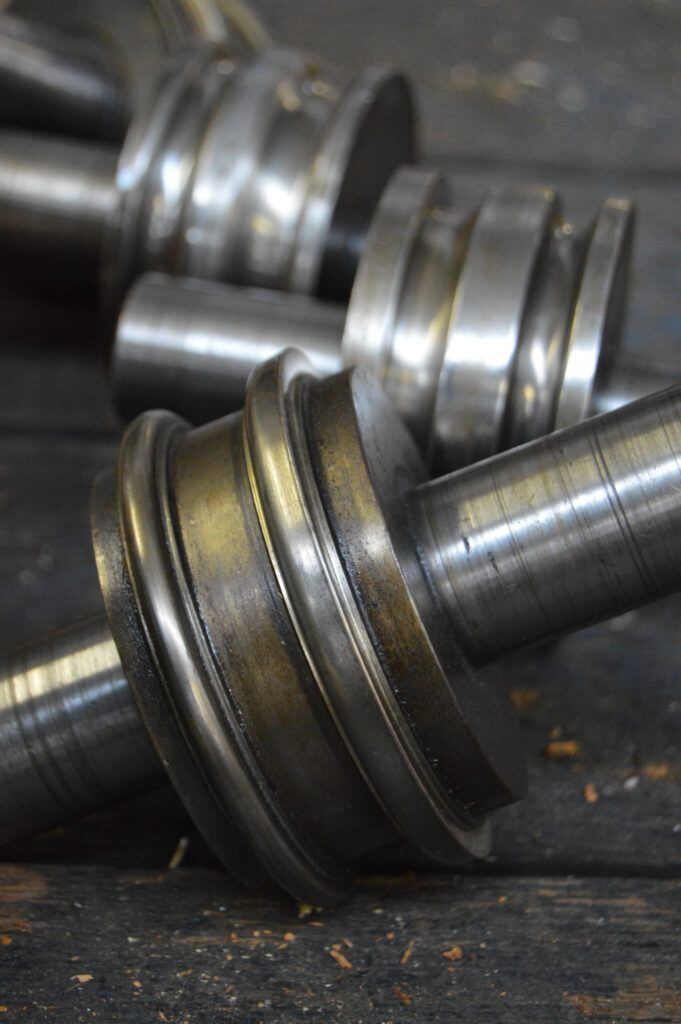
WHY DAHLSTROM?
Dahlstrom Roll Form has created superior custom roll formed products since 1904.
Along with consistently producing the highest-quality components in an ISO 9001:2015 facility, Dahlstrom offers the following services to all of our customers:
- Dedicated account managers
- Personalized quarterly reviews
- 99.5% on-time delivery commitment
- Custom vendor-managed inventory
- Expert tool design & part optimization
- Pass-through raw material pricing
- Tailored packaging & logistics
- Minor assembly & washing
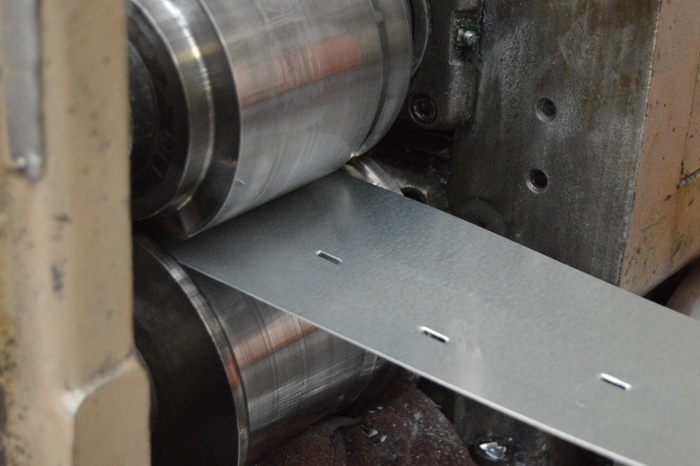
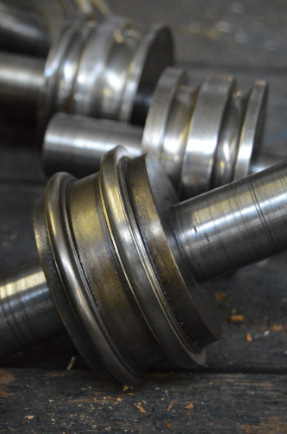
Recent Posts
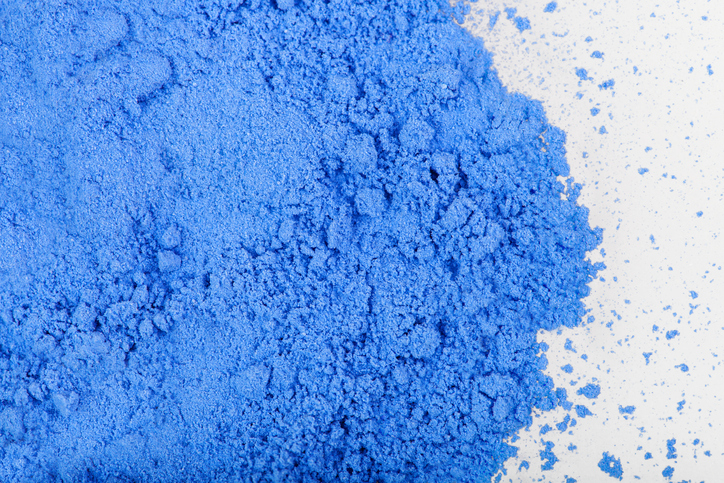
Industrial Powder Coating vs. Paint for Roll Formed Parts
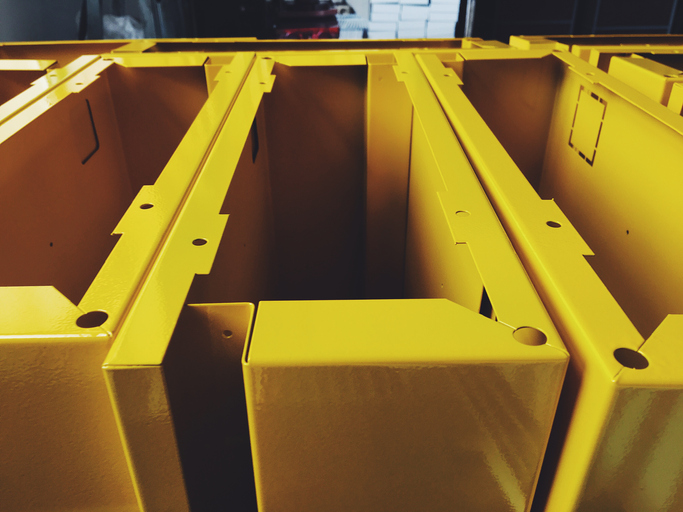
Goodbye Gray: Powder Coated Steel Roll Formed Parts
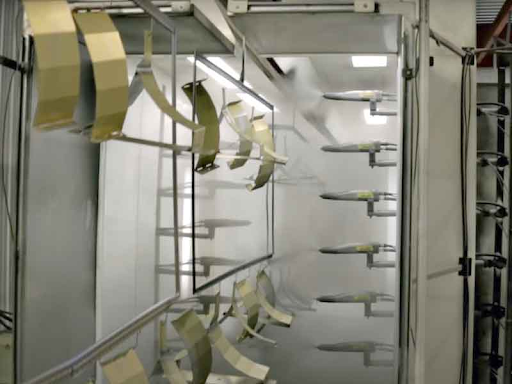