Solar Panel Racking
Solar energy’s expansion depends on roll formed mounting racks, which secure panels efficiently and cost-effectively to support industry success.
Solar Panel Racking | Frames & Structural Components
Solar energy is experiencing a booming trend in the US, with impressive annual growth rates surpassing 40% for the past decade. Experts predict this exciting momentum will continue.
Roll forming technology has played a vital role in making solar power both more viable and affordable. By employing roll formed parts, solar installers can securely position solar panels at optimal angles for extended periods of time. This innovation not only ensures long-term efficiency but also contributes to the low production costs that are crucial for the booming solar industry. Embracing roll formed solar panel mounting rack systems is an essential step toward a sustainable and prosperous future.
Roll forming offers advantages over extrusion for many components used in solar panel racking systems. We can roll form components in aluminum, galvanized, stainless steel, copper, brass, and recycled materials. Dahlstrom regularly produces structural elements in materials that meet ASTM standards for corrosion resistance. We can produce components with notches, slots, and/or holes to facilitate field assembly and adjustment.
Roll Forming Advantages
Both the commercial refrigeration and HVAC industries need a high volume of long, slender parts – roll forming’s specialty. Roll forming is a highly repeatable process. Once the tooling is in place, roll forming produces components more consistently than other metal shaping processes, even over long runs.
Whether the parts you need are decorative or structural, HVAC and commercial refrigeration parts are perfect for roll forming.
Roll forming allows engineers and designers to create customized components. Whether you’re using stainless steel parts for framing or pre-painted aluminum sheets for decoration, roll forming produces a clean and attractive finish.
Have a complex design? Roll forming can fabricate parts with:
- Complex profiles
- Inline punching for accepting mating parts
- Tricky hole patterns
- Tight tolerances
- Pristine finishes
Hole punching, bending, and cutting to length can easily fit into one continuous process rather than separate steps. Roll forming is a more cost-effective and productive method in all these cases.
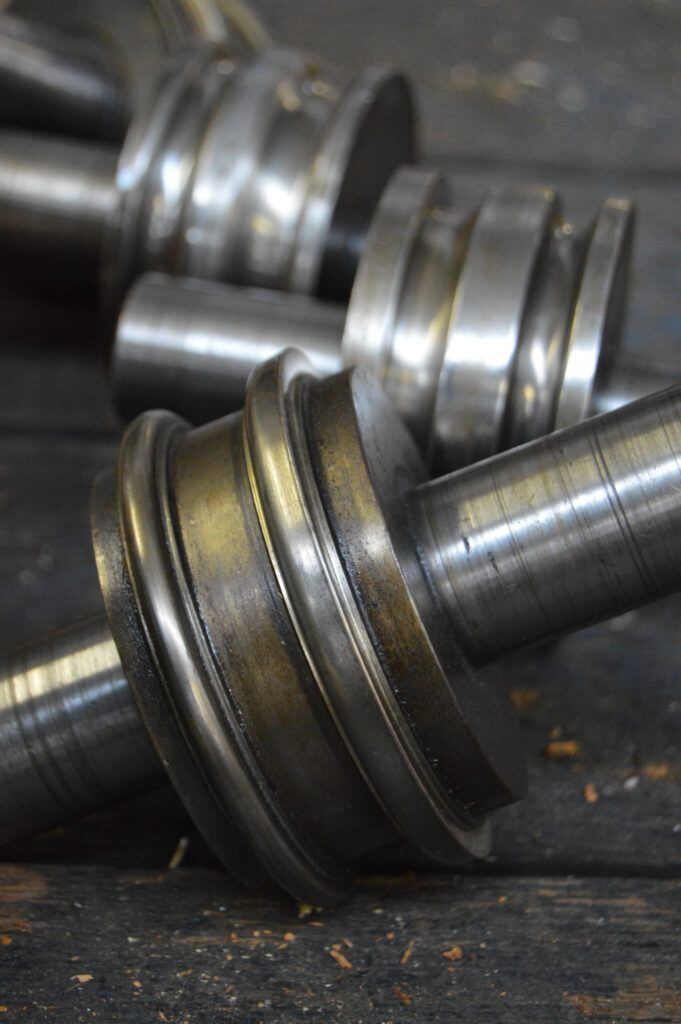
WHY DAHLSTROM?
Dahlstrom Roll Form has created superior custom roll formed products since 1904.
Along with consistently producing the highest-quality components in an ISO 9001:2015 facility, Dahlstrom offers the following services to all of our customers:
- Dedicated account managers
- Personalized quarterly reviews
- 99.5% on-time delivery commitment
- Custom vendor-managed inventory
- Expert tool design & part optimization
- Pass-through raw material pricing
- Tailored packaging & logistics
- Minor assembly & washing
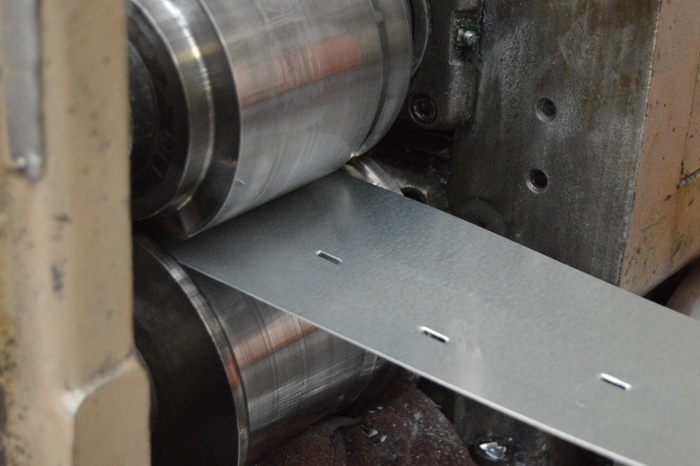
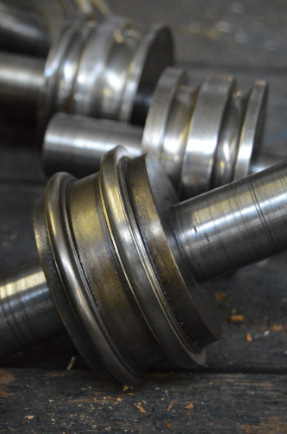
Recent Posts
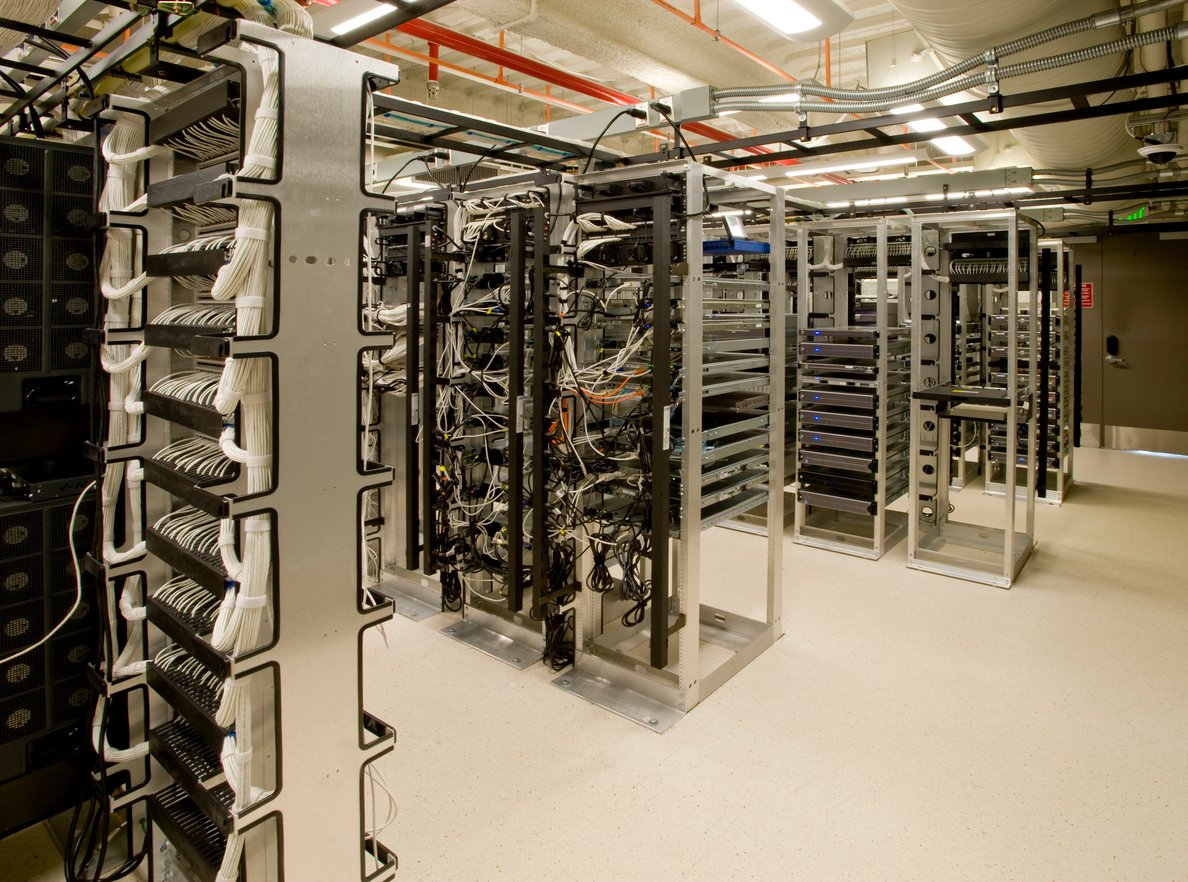
Slim‑Profile Battery Shielding Rails for UPS Rooms
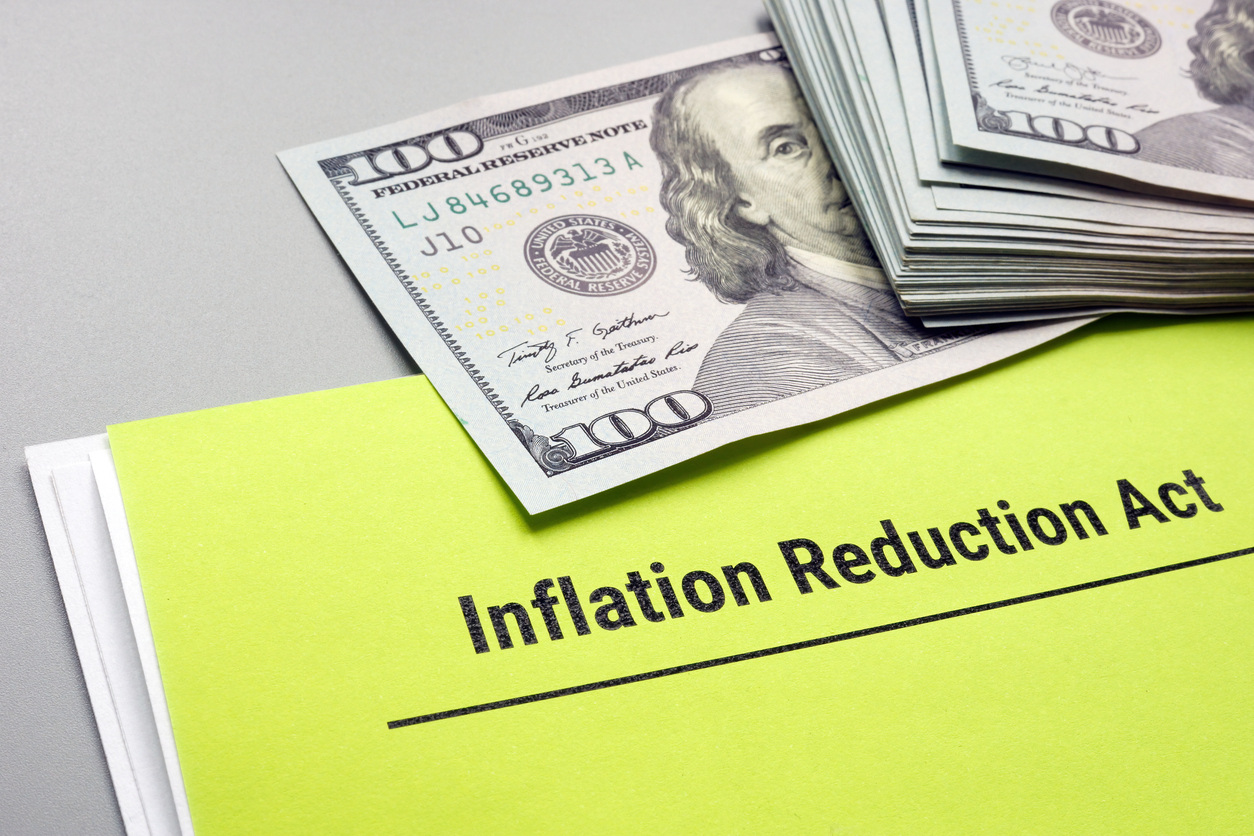
IRA Strengthens Customer–Metal Roll Former Partnerships
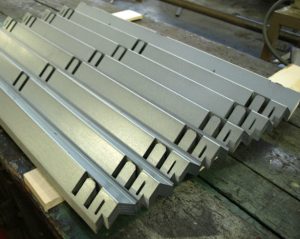